Manufacturing: Improve your supply chain and production processes with workflow automation
Table of contents
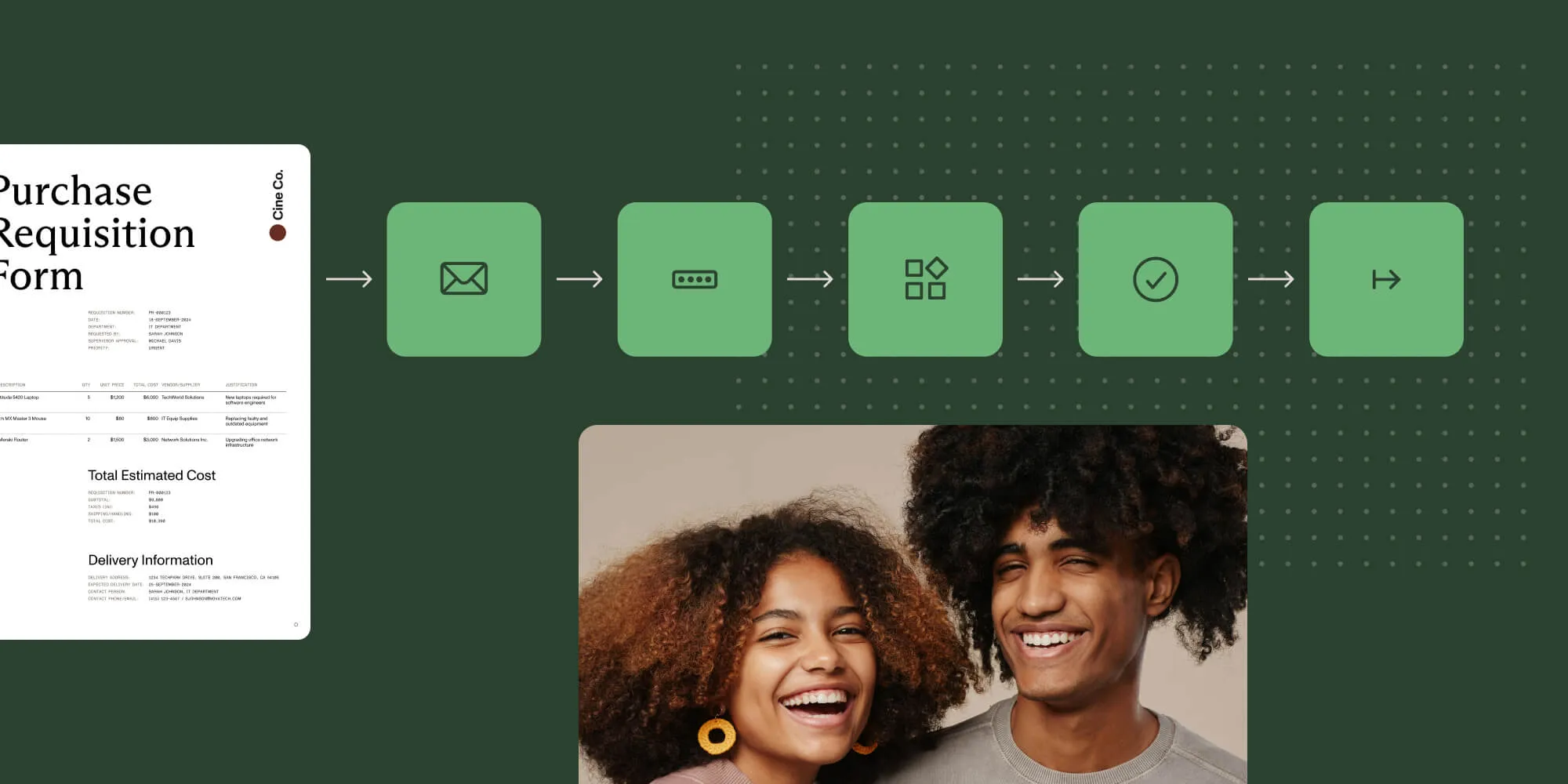
Try Workflow Automation free for 14 days
The manufacturing industry has never been more competitive. In today’s landscape, the most successful players know the key to beating the competition is optimizing every process — from procurement to production planning to quality control — to create the most efficient workflows possible.
Given all of the technological advances in the manufacturing space, creating the most efficient workflows possible absolutely requires embracing workflow automation.
Automation has the power to completely revolutionize manufacturing operations, in turn streamlining processes, improving efficiency, and empowering teams to do their best work — all of which can give manufacturers an edge in today’s hyper-competitive market.
But what does workflow automation in manufacturing look like? What issues can it improve (or, in many cases, solve) for manufacturers? And how can you start implementing automation within your organization and reaping the rewards that go along with it?
The manufacturing process maze: Understanding workflow challenges
Before jumping into how workflow automation can change the game for manufacturers, this section will quickly touch on the specific complexities of manufacturing workflows.
Manufacturers face a number of unique, industry-specific workflow challenges.
- Complex, interconnected processes — Unlike more straightforward workflows, manufacturing typically involves a number of interconnected processes that need to work together seamlessly for manufacturing to happen. Take production scheduling as an example. It seems simple, but in actuality, scheduling requires considering and simultaneously balancing a variety of factors, such as machine capacity, labor resources, and customer deadlines. If one factor is missed or off-balance, the schedule can be thrown off. When something is off with production scheduling, it can then throw off all the processes that process is connected to (like production, quality testing, and customer delivery), negatively impacting the entire manufacturing cycle.
- Multiple stakeholders across different departments — Manufacturing workflows often involve stakeholders from various departments, all of which have their own priorities, systems, and processes. For example, procurement teams focus on cost and supplier relations; production managers prioritize equipment utilization and output; quality assurance teams are in charge of regulatory compliance; and engineering staff manage product specifications and improvements. Coordinating all these stakeholders effectively can be a huge challenge, as each is focused on their own specific goals and metrics. This is especially true when conflicting priorities arise. For example, engineering may want to switch materials to improve a product, but procurement may not be able to secure that material within the project budget.
- Material issues — To manufacture goods, you need the materials for production, and securing those materials can be a real challenge. Materials often have varying lead times, with some components available within days, while others might take weeks, which can throw a wrench in manufacturing processes. Prices can also be an issue: Material prices can change rapidly, which can force manufacturers to adjust their procurement strategies in real time.
- Global supply chain complexity — The supply chain — and in particular the global supply chain — also creates complexities within manufacturing workflows. For example, working with teams and suppliers across different regions and countries presents its own challenges, like time zone differences, language barriers, and regional business practices or norms. Plus, moving materials across international borders means navigating complex shipping regulations and customs procedures.
How manual processes hold manufacturers back
It’s clear that the manufacturing industry presents undeniably complex challenges. But all of those challenges can be effectively addressed and managed with the right processes in place.
However, when it comes to manufacturing workflows, not all processes are created equal. Many manufacturers still rely on manual processes to manage their manufacturing workflows — an approach that can have a serious impact on workflow efficiency.
Some of the challenges created by managing manufacturing processes manually include:
- Information silos and communication gaps — With manual, paper-based processes, data and information aren’t easily accessible across an organization. That lack of accessibility can wreak havoc on workflows. For example, when production teams lack visibility into inventory levels, the result can be under or overproduction. If engineering changes don’t reach affected departments in real time, out-of-date products may continue to be manufactured. The point is, when processes are handled manually, information access is restricted, which creates issues like wasted materials, misalignment or miscommunication between teams, and missed improvement opportunities.
- Delayed approvals — Paper-based approval processes can slow down operations in a major way. Chasing down signatures — whether for a purchase requisition, engineering change, or other manufacturing-related document — can be time-consuming. Often, documents will sit on an approver’s desk for days or weeks longer than necessary. This can create serious bottlenecks in the approval and decision-making processes, and because there’s no digital trail for each document and where it is in the process, it can also be extremely easy for things to fall through the cracks, causing further holdups.
- Increased risk of data entry errors — It doesn’t matter how on top of things your employees are; they’re humans, and humans make mistakes, including with data entry. When your team is manually entering data into systems, or transferring data from one system to another, it creates ongoing opportunities for mistakes that can cost your business time and money. For example, a transcription error in a purchase order can lead to the wrong supplies being ordered, or a manual inventory count can lead to an incorrect view of how much inventory you actually have on hand. These errors create waste, quality problems, and cost overruns, and they ultimately damage customer relationships.
- Redundancies and missed opportunities to spot problems — When you rely on manual processes — and only have access to certain information at certain times — connecting the dots and spotting issues before they turn into bigger problems is a challenge. For example, if you don’t have access to real-time inventory data, you might not immediately realize that you’re running low on a certain material and need to place an order, which can hold up production. Manual processes can also cause redundancies. For example, say QA manager A has already quality tested a product, but the report is sitting on the QA director’s desk, waiting to be approved and manually entered into the system. But if QA manager B doesn’t know the testing has already been done — and there’s no documentation in the system to confirm the work has been completed — they might decide to tackle testing themselves, wasting time and resources.
- Inconsistencies — Manual processes, by design, create opportunities for inconsistencies. For example, employees may interpret, approach, and document processes differently. Team members may skip certain steps or leave fields on documents blank. And those inconsistencies can create a variety of issues, like non-compliance with regulatory requirements or incomplete or inaccurate data for reporting or auditing purposes.
How workflow automation transforms manufacturing operations
The good news is that workflow automation in manufacturing effectively solves all the issues manual processes create while also making workflows more efficient, streamlined, and clear.
Creating automated digital workflows in manufacturing can improve operations in a variety of areas, outlined below.
Improved supply chain management
As mentioned, supply chain management is one of the more complex challenges in the manufacturing space. Automated supply chain processes offer a variety of improvements over their manual counterparts, including:
- Streamlined procurement — With automated systems, you can automatically route procurement documents like purchase requisitions to approvers, track them throughout the process, and send reminders if and when approvers are taking too long to sign off. This streamlines the procurement process and eliminates the bottlenecks and delays that often come with manual approvals.
- Better inventory management — Instead of realizing you’re running low on materials when it’s already too late, automated systems can track inventory levels in real time and automatically trigger reorders when supplies hit preset levels. This can help minimize emergency orders and/or production delays — both of which can be extremely costly.
- Improved supplier management — With manual processes, it can be hard to generate the data you need to fully understand your supplier relationships, which are the most beneficial for your business. But with automated systems, you can track supplier performance metrics over time, like delivery times or product quality, giving you access to data you can use to better evaluate and manage your supplier relationships.
- Material forecasting and pricing insights — Automation helps tackle material issues by monitoring market trends and supplier pricing in real time; when material costs fluctuate, automated systems can alert purchasing teams, allowing them to consider alternative suppliers or materials or pull resources from elsewhere, which can help keep production within budget.
- Better global supply chain management — For manufacturers working with global supply chains, automation can bridge a variety of related issues, like time zone and language gaps — making for easier and more effective supply chain management. For example, automated translation features, time zone-aware notifications, and standardized documentation can make working with international suppliers much smoother, while automated customs documentation can help streamline complex international shipping procedures.
Bridging departmental divides
As mentioned, one of the biggest challenges in manufacturing operations is coordinating multiple stakeholders across different departments. Workflow automation addresses this directly.
- Create unified platforms — Instead of each department working in their own systems and with their own goals, automated workflows create a shared platform where engineering, production, procurement, and quality teams can all see how their work affects others. This removes information silos and creates alignment across departments.
- Balance competing priorities — Automated systems help manage those inevitable situations when different departments have conflicting needs or goals. The platform brings all relevant data and perspectives into one place, making tradeoffs more transparent and decisions more collaborative. For example, if engineering wants to change materials, but procurement has money worries, the automated system gives both teams a clear, data-driven view of the technical benefits and financial effects. This makes it easier to find solutions that work across departments.
- Collaborate cross-functionally — Automated workflows make it clear who needs to do what and when, streamlining collaboration between departments. For example, when production needs input from quality and engineering, the system can notify everyone simultaneously and track responses — without the need for followup emails or meetings. This can make collaboration easier, more effective, and less time-intensive.
Streamlined manufacturing AP automation in construction
For manufacturers that work in the construction space, automation in the construction industry can be extremely helpful, particularly when it comes to accounts payable (AP).
Construction AP automation can streamline processes through several key mechanisms.
- Efficient invoice processing — Automated systems can capture invoice data directly from emails or supplier portals, eliminating those mind-numbing hours of typing invoice data into your system (and dealing with all the errors that come with it).
- Improved approval routine — Instead of invoices getting lost in someone’s inbox or in paper-based systems on their desk, automated workflows allow you to immediately and automatically route bills to the right approvers. This ensures you get approvals when you need them. Plus, the system can automatically send reminders when someone’s taking too long, eliminating the need for followups.
- Three-way matching — Three-way matching(opens in a new tab) is an automated process that compares purchase orders, invoices, and receipts or receiving documents to ensure they all match up. This process can flag inconsistencies — for example, an overcharge — helping you spot AP issues before they become bigger or more difficult to manage.
- Comprehensive audit trails — Digital trails record every step of the approval process — who looked at what, when they approved it, and why. This can help keep stress levels low and make information easier to find during audits and/or tax time.
Enhanced production efficiency
Workflow automation can also help to optimize the production process, improving production efficiency and reducing bottlenecks and/or delays in a variety of ways.
- Integrated production planning — Automated production planning tools consider everything at once — your materials, machine capacity, worker availability, deadlines, and more — allowing you to create realistic schedules based on your available resources.
- Real-time production visibility — Real-time monitoring lets you see exactly how production is progressing and how that progression lines up against your projected schedule. The benefit? Instead of discovering at the end of the day or week/month/quarter that you’re behind, you can catch and fix issues as they happen.
- Streamlined machine maintenance — Instead of waiting for equipment to break down (which usually happens at the worst possible time), automated maintenance workflows help you send service requests and stay on top of scheduled maintenance and repairs. This will reduce product interruptions and costly emergency fixes.
- Fewer production redundancies — Automated systems create a single source and record of all production activities. Everyone within the organization can see what’s been done, which eliminates redundancies and saves time, materials, and potential frustration. For example, no more duplicate quality tests because teams didn’t know testing was complete and the testing report is sitting on someone’s desk; it’s all there, in real time, in the automated system.
Improved quality control and compliance
Automation also helps better manage quality control and production-related documentation, streamlining compliance and ensuring consistency across the organization through the following methods:
- Standardizing quality checks — Digital forms ensure everyone follows the same quality inspection steps and documents them in the same way — no more differences between shifts, locations, or individual inspectors/workers. The result? More consistent quality and fewer “it depends who checked it” inconsistencies.
- Problem resolutions — When quality-related issues do pop up, automated workflows guide everyone through the proper steps on how to handle those issues, like documenting the issue, investigating root causes, implementing fixes, and filling out the right paperwork. This not only creates a paper trail for each incident, but it also improves compliance.
- Improved record-keeping — Automated industrial document management software allows you to create consistent digital records for all production-related documents. This can improve regulatory compliance and make documents easier to organize, search, and maintain, reducing administrative burden and ensuring your team can access the documents they need, when they need them.
- Enforcing process consistency — Remember those inconsistencies we mentioned with manual processes? Automation eliminates them by enforcing the same steps, documentation requirements, and approval flows every single time, regardless of who’s handling the process.
- Faster approvals — Paper-based approval processes can take too long, and it’s easy for things to go wrong. For example, you might miss an important signature or an approval that gets stuck on someone’s desk or takes longer than needed. Automated systems make the approval process easier. They have features like reminders, reviews, and signatures at the same time, and document tracking. This lets people who approve things see exactly where things are at every step of the process.
Accelerated engineering change management
Engineers play a hugely important role in the production process, continually improving, changing, and optimizing processes. Workflow automation in manufacturing can help ensure that engineering changes integrate seamlessly into existing processes and operations.
- Keep everyone in sync with changes — When product or process changes happen, automated workflows ensure everyone affected gets notified of the changes in real time — preventing situations where production is using one version while engineering has moved on to another.
- Eliminate version confusion — Automated systems track every document version and update, so you never have to guess which version is the latest and which version production should be using. This eliminates uncertainty and ensures no one has to waste time version-checking — for example, reviewing and comparing file dates.
Best practices for implementing manufacturing workflow automation
Considering implementing workflow automation in your manufacturing operations? Be sure to keep these best practices in mind:
- Start with process mapping — Before you move forward with automated processes, make sure to thoroughly document your current workflows and identify any existing pain points, bottlenecks, and/or inefficiencies. This will help you not only determine which processes to automate first, but also help you define what problems need to be solved and ensure you choose an automation solution that addresses those specific problems.
- Focus on high-impact processes first — Trying to automate everything at once can cause more issues than it solves. For example, teams may struggle to learn the ropes of the automated platform or keep up with all the changes in processes. So, if you want your implementation to be successful, start slow and give your team time to acclimate. Start with the processes that are causing the most issues or offer the greatest potential for real, measurable change in your organization. Invest in training your team on the new processes. Then, once you’ve successfully implemented automation where it matters most — and gotten your team on board — you can move on to automating additional processes within the manufacturing cycle.
- Involve frontline workers — The people who perform the work daily often have the best insights into how processes could be improved. Make sure to include frontline workers in the automation design process. That way, you can ensure your automation efforts address the issues your team struggles with most.
- Plan for integration — Any automation solution you choose should work with your current systems. For example, your enterprise resource planning (ERP), quality management, or design software should work with it. When these systems integrate, it creates more consistent, streamlined workflows, and it also eliminates redundancies — for example, having to enter data into multiple systems.
- Design for scalability — Have plans to grow in the future? If so, it’s important to choose an automation platform that can grow along with you without any major growing pains. For example, look for automation platforms that allow you to add new workflows and users without having to go through any major reconfigurations.
For more ideas to prepare to implement workflow automation in your manufacturing processes, check out our helpful article on how to define your process before automating workflows. Once you’re ready to get started, our free trial of Nutrient Workflow is just a click away!